Precision in Oil & Gas Machining Services
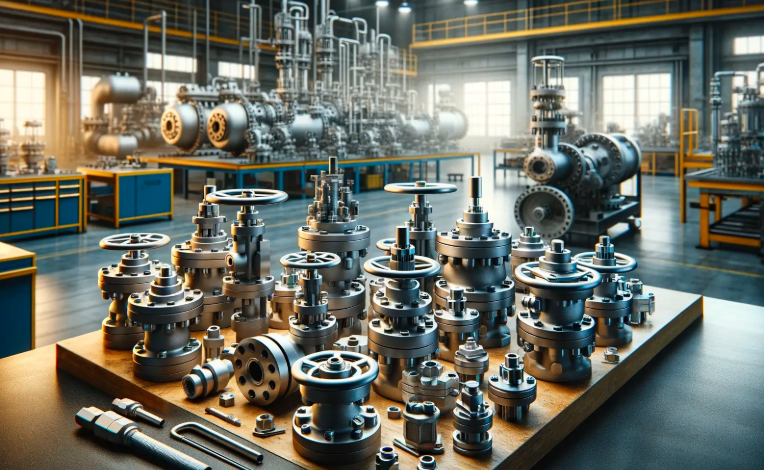
The oil and gas industry relies on high-performance components that must endure extreme operating conditions. From deep-sea drilling to high-pressure refining processes, every piece of equipment used in this industry must be accurate, durable, and reliable. This is where oil & gas machining services play a critical role. These specialized machining services provide precision-engineered parts that meet strict industry standards, ensuring the efficiency and safety of oil and gas operations.
This article explores the importance of machining services in the oil and gas sector, the techniques used, key components produced, and the challenges faced in manufacturing.
The Importance of Machining Services in Oil and Gas
The oil and gas industry requires high-strength materials and precise fabrication techniques to create components that can withstand high temperatures, extreme pressures Oil & Gas Machining Services and corrosive environments. Machining services play a crucial role in meeting these demands.
1. Ensuring High Precision
Precision is vital in oil and gas equipment. Any deviation in dimensions can cause leaks, inefficiencies, or failures. Machining services use computer-controlled equipment to ensure tight tolerances and perfect fittings.
2. Durability and Longevity
Machined components must endure harsh environmental conditions. High-quality machining processes improve the durability, wear resistance, and longevity of these parts.
3. Custom Fabrication
Every oil and gas operation is unique. Custom machining services allow companies to design and produce components tailored to specific project requirements.
4. Cost-Effective Production
Advanced machining techniques reduce material waste and rework, making manufacturing more cost-efficient. Automated machining also reduces labor costs and improves productivity.
Types of Machining Techniques Used
Oil & gas machining services involve various precision manufacturing processes to produce components that meet industry standards. Some of the most commonly used machining techniques include:
1. CNC Machining
Computer Numerical Control (CNC) machining is the backbone of oil and gas manufacturing. It involves computer-controlled cutting tools that shape raw materials into precise components. CNC machining ensures high accuracy, repeatability, and efficiency.
2. Turning
This process is used to create cylindrical parts such as pipes, rods, and flanges. A rotating workpiece is shaped using cutting tools to achieve the desired dimensions.
3. Milling
Milling removes excess material from a workpiece using rotating cutting tools. It is commonly used to create complex shapes and flat surfaces on components like valve bodies and pump casings.
4. Drilling and Boring
Drilling creates precise holes in metal components, while boring enlarges these holes to ensure tight fits and proper alignment. These techniques are essential for pipe connectors and wellhead equipment.
5. Grinding and Polishing
Grinding is used for finishing surfaces with high precision, ensuring smoothness and removing imperfections. Polishing further enhances the corrosion resistance of metal parts.
6. Welding and Fabrication
Many oil and gas components require welding and fabrication for assembly. High-quality machining and welding ensure the strength and durability of critical structures.
Common Materials Used in Oil & Gas Machining
The choice of material significantly impacts the performance and lifespan of machined components. The most commonly used materials in oil & gas machining services include:
1. Stainless Steel
- Resistant to corrosion and high temperatures
- Used for valves, pipelines, and storage tanks
2. Inconel
- High strength and excellent oxidation resistance
- Ideal for high-pressure environments and extreme heat conditions
3. Titanium
- Lightweight yet strong
- Used in offshore drilling equipment and deep-sea exploration tools
4. Carbon Steel
- High durability and strength
- Common in casing, tubing, and structural components
5. Aluminum
- Lightweight and resistant to chemical corrosion
- Used in pump housings and machinery supports
Key Components Produced in Oil & Gas Machining
Oil & gas machining services manufacture a wide range of components essential for drilling, refining, and transportation. Some of the most critical parts include:
1. Drilling Equipment
- Drill bits: Machined to ensure precision cutting through rock formations.
- Mud motors: Essential for downhole drilling operations.
2. Valves and Fittings
- Ball valves, gate valves, and check valves are machined to control fluid flow in pipelines.
- Fittings and connectors ensure leak-proof connections between components.
3. Wellhead Equipment
- Flanges, seals, and casing heads are manufactured with tight tolerances to handle extreme pressures.
4. Pipeline Components
- Manifolds, couplings, and reducers are machined to precise specifications for safe oil and gas transportation.
5. Pump and Compressor Parts
- Pump impellers, housings, and shafts are machined for maximum efficiency and durability.
6. Blowout Preventers (BOPs)
- Used as safety devices in drilling operations to prevent uncontrolled pressure releases.
Challenges in Oil & Gas Machining Services
Despite its importance, machining for oil and gas faces several challenges:
1. Machining Tough Materials
Hard metals like Inconel and titanium require specialized cutting tools and cooling techniques to prevent tool wear.
Read also: The Rise of Blank Apparel: A Fashion Essential
2. Meeting Strict Industry Standards
Every component must comply with API (American Petroleum Institute), ISO, and ASME standards, which require rigorous quality control and inspections.
3. Managing High Costs
The complexity and precision of oil and gas components make machining expensive. However, automation and optimized processes help control costs.
4. Harsh Operating Conditions
Machined components must endure corrosion, extreme pressures, and temperature fluctuations, requiring advanced coatings and surface treatments.
5. Supply Chain Challenges
Delays in material sourcing, transportation, and logistics can impact project timelines. Efficient supply chain management is crucial.
Future Trends in Oil & Gas Machining Services
The industry is evolving with new technologies and innovative machining solutions to improve efficiency and sustainability.
1. Automation and Smart Machining
Advanced CNC automation reduces human error and increases production efficiency. AI-driven monitoring systems can detect machine wear and maintenance needs in real-time.
2. Hybrid Manufacturing
The combination of additive manufacturing (3D printing) and CNC machining allows for rapid prototyping and custom component production.
3. Advanced Surface Treatments
New coatings like ceramic and plasma nitriding improve wear resistance and corrosion protection, extending component lifespan.
4. Eco-Friendly Machining
Sustainable manufacturing techniques focus on reducing energy consumption and minimizing material waste, aligning with environmental regulations.
Conclusion
Oil & gas machining services play a critical role in ensuring the reliability, efficiency, and safety of oil and gas operations. Through precision machining, durable materials, and advanced manufacturing techniques, the industry continues to develop high-quality components that meet demanding operational needs.
Despite challenges such as high costs, tough material machining, and regulatory compliance, innovations in automation, AI-driven machining, and hybrid manufacturing are shaping the future of the sector. With continued advancements, oil & gas machining services will remain at the forefront of energy industry advancements, providing high-performance solutions for drilling, refining, and transportation operations.